Pet Food Manufacturer reduces give-away by up to 5 tonnes per day
A pet food manufacturer ordered a Minebea Intec Flexus® twin lane checkweigher that was custom built to their exact requirements to help reduce give-away and increase efficiencies.
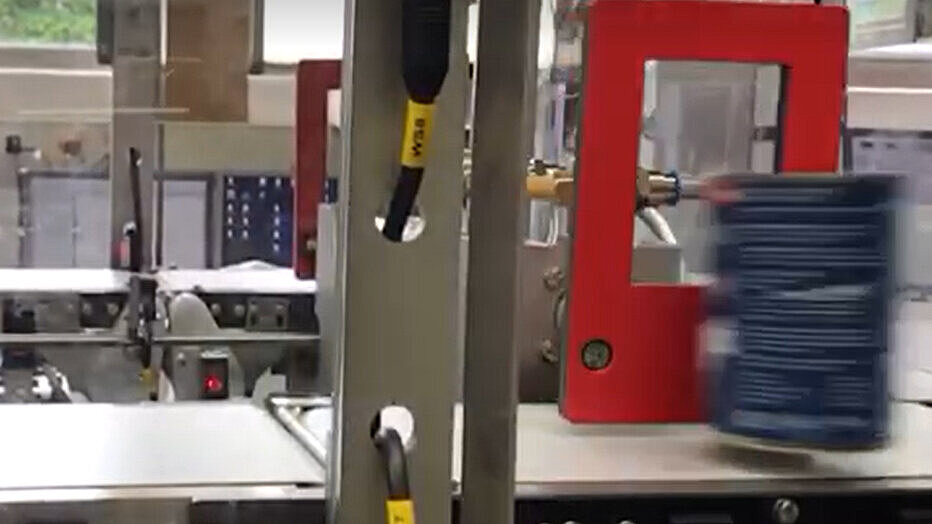
Key facts
The Flexus® has reduced give away for the customer by up to 5 tonnes per day. It has also negated the requirement for offline sampling, reducing staff time and costs
Application & Product
The Flexus® twin lane checkweigher was built to the customers exact specification to ensure seamless integration into their existing manufacturing line, including spacing of the twin lanes to match existing conveyors which saved time and money in reconfiguring them. The Flexus® offers high speed checkweighing; rejects products that don’t meet the minimum fill level and automatically controls the fill level up stream.
- Flexus® twin lane checkweigher with reject arm with custom converging conveyor
Customer benefits
- Reduced give-away, automated checkweighing, automated fill-level adjustment and reduced staff costs are all benefits for this customer as a result of the Flexus® twin lane checkweigher.
This particular customer had noticed that all the tins of pet food they were manufacturing were being over-filled at a time when key ingredients were rising in cost due to home cooking and the influence of TV chefs in the pandemic whilst at the same time pet ownership was increasing and therefore demand for pet food rising. To reduce the overall give-away, the customers goal was to reduce the weight of each tin of pet food by 3g by weighing every tin and using the statistics to control the can fillers. The customer had been conducting random offline sampling using a Minebea Intec Combics® scale linked to the SPC@Enterprise software system. Data from this system highlighted that the high level of give-away combined with the high cost of ingredients meant it was necessary to introduce a better system to control give-away.
In response to the customers’ requirements, Minebea Intec recommended a high speed checkweigher to remove the requirement for sampling by checking the weight of each can and reducing give away to an absolute minimum. A bespoke twin lane machine was built with spaced lanes to meet the incoming conveyors on the existing line then after weighing we supplied a system to converge all the tins back into one line. The newly built checkweigher weighs 12.5 cans a second, it rejects any under-fills, controls the can fillers and is also connected to the same SPC@Enterprise data capture system which compared the before and after activity and the volume of product that has been saved by the new checkweigher. Customers of over 20 years are delighted that they’re now saving 5 tonnes of give-away every day
Mediacenter
Category | File Name | File Size | File Type | ||
---|---|---|---|---|---|
Best Practices | |||||
Best Practices | Best Practice // Pet Food Manufacturer reduces give-away by up to 5 tonnes per day | 641 KB |