Weighing and inspection Wiki
Accuracy is essential in weighing and inspection solutions - but it is not easy to keep track of the multitude of technical terms. In the knowledge database you will find all relevant terms explained in an easy-to-understand way.
Browse through our category pages, use the keyword search or use the alphabetical overview to get more information on over 150 technical terms.
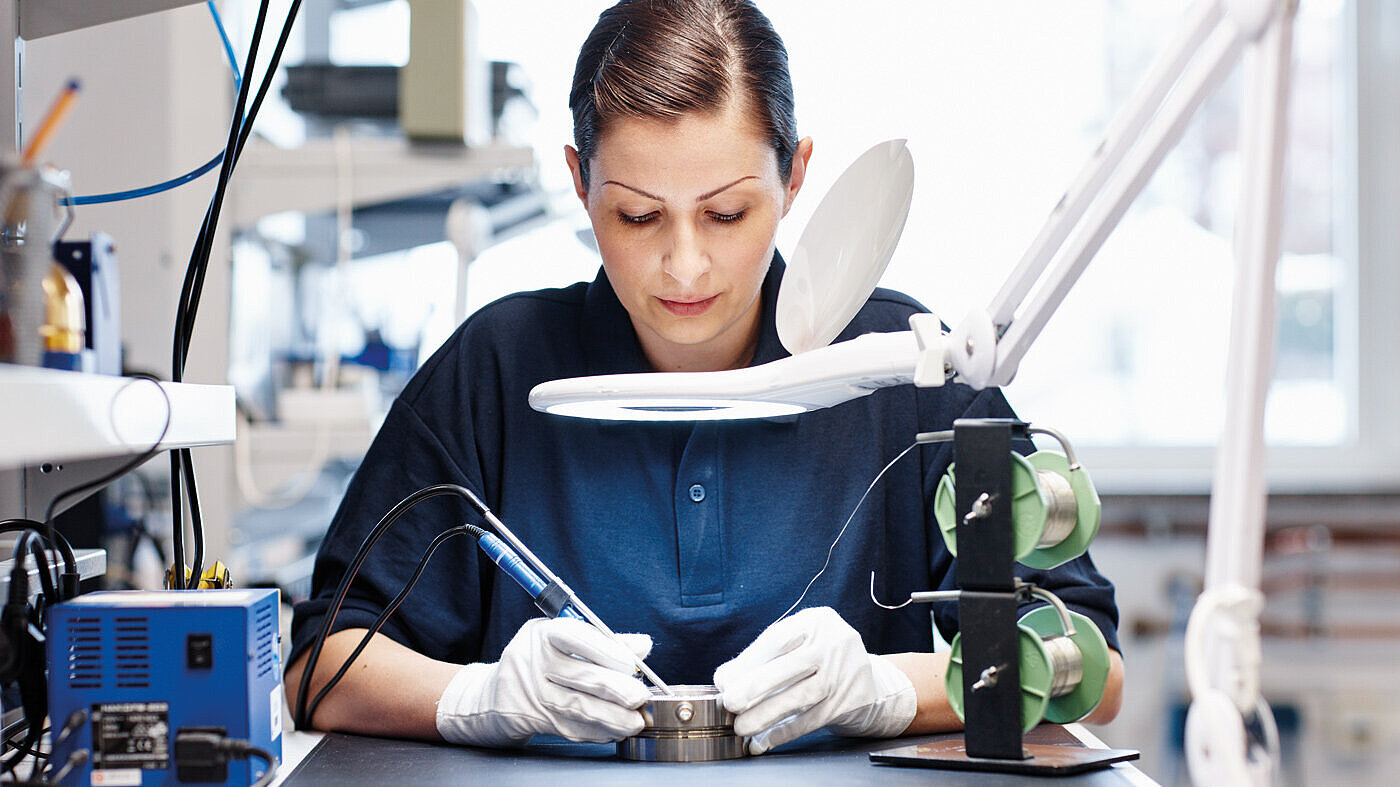