De réelles économies via la détection à rayons X
Comment la détection des rayons X permet de passer à un emballage recyclable et de réduire les déchets.
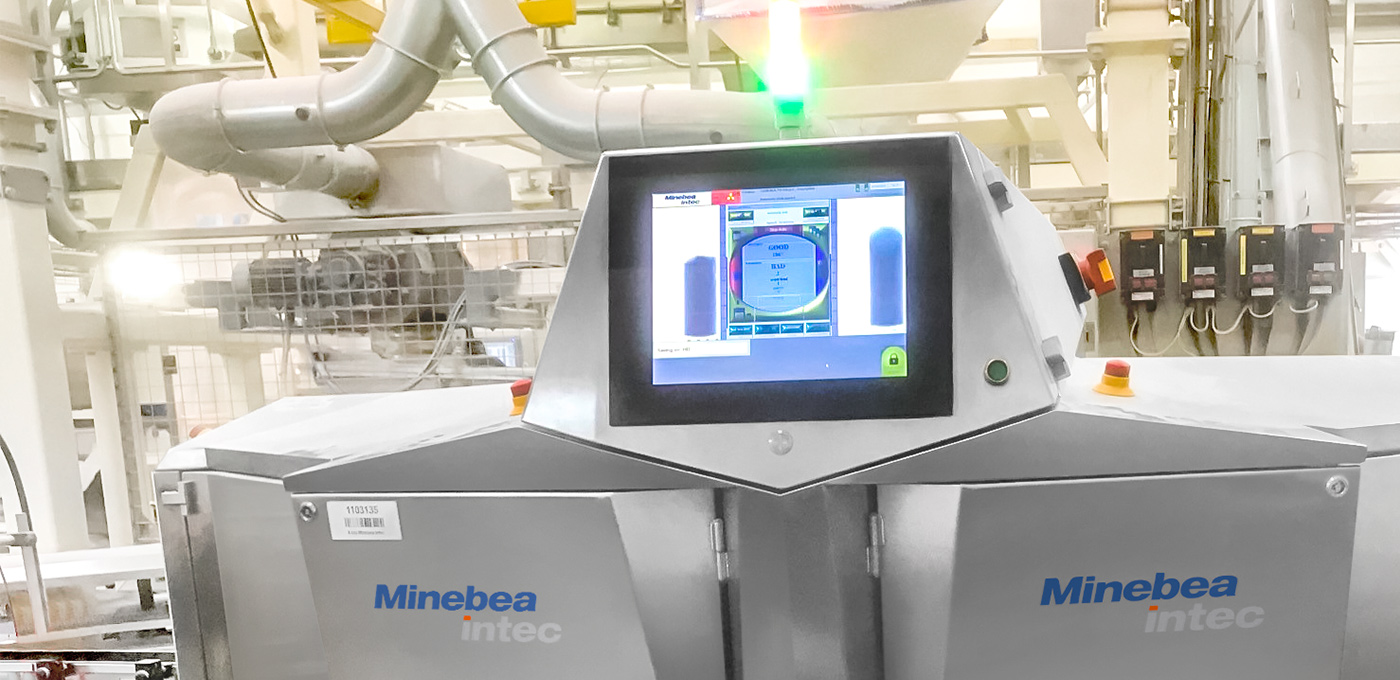
Données essentielles
Premier Foods, Knighton, fabricant de produits alimentaires, mélange, transforme et emballe des aliments et boissons en poudre tels que crème anglaise, lait écrémé en poudre et cacao en poudre.
Application & Produits
Premier Foods, Knighton a opté pour des tests en fin de ligne avec le système à rayons X Dymond S qui scanne les produits emballés complets et remplace l’ancien détecteur de métaux qui réalisait des tests toutes les heures sur les produits en vrac. Une méthode onéreuse et g é nératrice de déchets.
Avantages pour le client
- La détection par rayons X en fin de ligne a éliminé les déchets et permis de réaliser des économies
- Le changement de solution d’inspection a largement réduit le travail de nettoyage et les coûts de matériel
« Minebea Intec nous a proposé la solution la mieux adaptée à nos besoins ; moins encombrant que les autres systèmes du marché, le concept unique du système à rayons X Sideshooter Dymond S est parfait pour notre ligne de production. Grâce à lui, nous économisons 80 000 £ par an et nous réduisons nos déchets tout en proposant un emballage 100 % recyclable. »
Lee Millward
Responsable de l’ingénierie chez Premier Foods, Knighton
Premier Foods, Knighton souhaitait passer à un emballage 100 % recyclable en remplaçant le fond métallique par du papier. Pendant cette transition, elle a de plus mis en place des tests en fin de ligne pour réduire les déchets générés par un détecteur de métaux en vrac placé plus en amont de la ligne. Grâce au Dymond S, l’entreprise a atteint ses deux objectifs tout en réalisant d'importantes économies annuelles.
Grâce aux rayons X, elle ne perd plus qu’un seul conteneur lorsqu’un rejet est détecté et peut utiliser les conteneurs pleins pour réaliser les tests de routine toutes les heures. La nouvelle méthode détecte non seulement le métal, mais aussi le verre, la pierre, etc. Lee Millward, Responsable de l’ingénierie chez Premier Foods, Knighton, explique : « La plage de détection du Dymond S est bien meilleure que sur l’ancienne méthode, avec notamment plus de portée sur les petits corps étrangers. »
Autre avantage : le gain de temps et les économies réalisées sur le nettoyage. Alors que les nombreux tuyaux de l’ancien système devaient être nettoyés (puisqu’ils testaient de la poudre), le contrôle actuel ne nécessite aucun nettoyage puisqu’il se fait sur des produits complets en conteneurs. De plus : « L’absence de déchets nous fait économiser 80 000 £ par an. En un an à peine, nous avons rentabilisé la machine. C’est un retour sur investissement impressionnant si l’on considère la durée de vie de la machine.
» Premier Foods, Knighton a aussi opté pour le service Premium Plus qui garantit un temps de réponse de 4 h. Les experts du service Minebea Intec sont disponibles 14 heures
par jour pour fournir un support technique exclusif, résoudre les problèmes et assister le personnel. Lee conclut : « C’est un 10/10 pour Minebea Intec. J’ai déjà recommandé cette machine à nos autres sites de fabrication. Le produit, le personnel et l’expérience en général sont parfaits. »
Mediacenter
Catégorie | Nom du fichier | Taille du fichier | Type de fichier | ||
---|---|---|---|---|---|
Best Practices | |||||
Best Practices | Bonnes pratiques // Une société agroalimentaire économise 80 000 £/an grâce aux rayons X de Minebea Intec | 784 KB |