X-ray solution in hygienic design
Fast and precise X-ray inspection solution convinces in food production
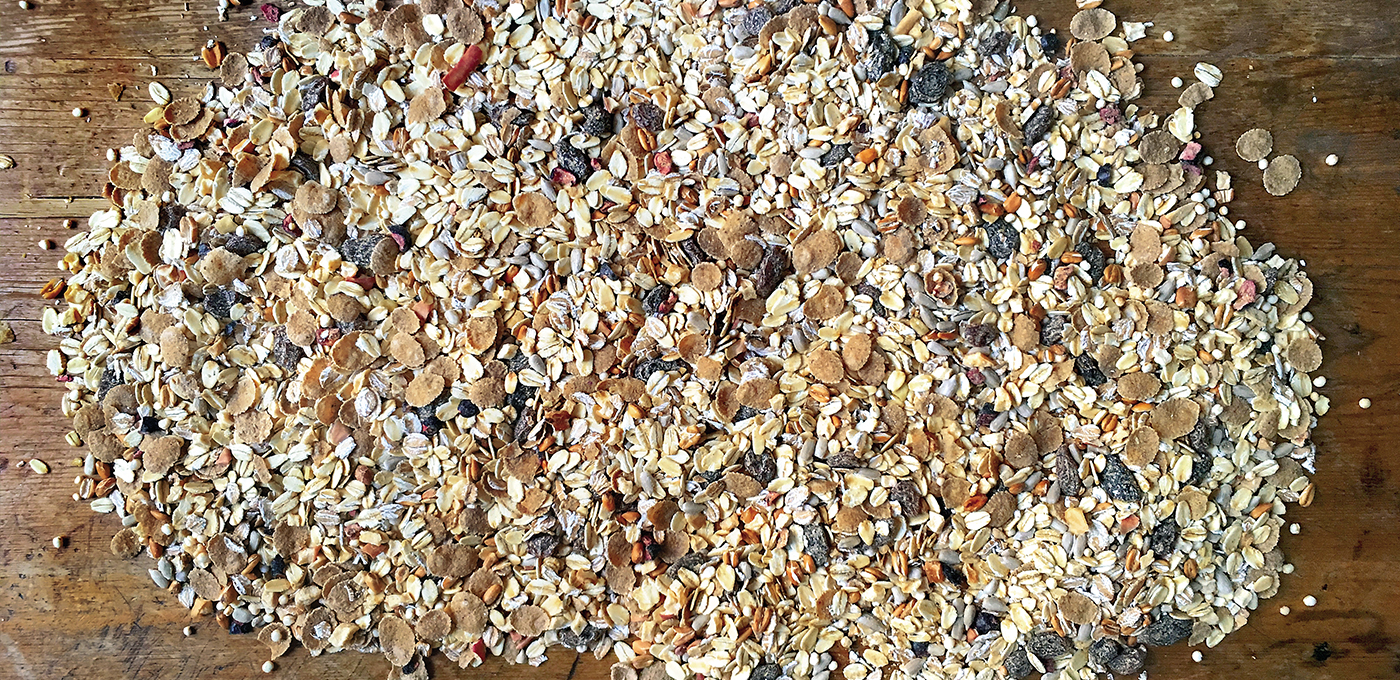
Key facts
Anona, based in Colditz, Germany, manufacturers food supplements as well as soups, cereal and ice cream products. Following a defect in the dosing system, the company was unable to rule out the possibility that the product had become contaminated. Anona decided to act, opting to install a fast inspection solution from Minebea Intec.
Application & Product
Plastic containers are filled with the finished product from raised bulk bags, which are then checkweighed and sealed with an aluminium lid.
Customer benefits
The X-ray inspection system Dymond guarantees the reliable detection of foreign objects, e.g. metal, ceramic, glass or plastic.
- Maximum detection sensitivity
- Hygienic design
The reliable service from Minebea Intec made it possible to inspect the batch in question in next to no time.
"Faults happen. What matters is how you handle the situation. Minebea Intec supported us 100 percent during the suspected contamination."
Ralf Wiedenbeck
Production Manager, Anona
At food manufacturer Anona, a defective machine in the dosing system led to the suspicion that a metal part may have found its way into the product during the filling process. The affected production line fills cans with powders, which are then sealed with an aluminium lid. It was therefore not possible to perform subsequent checks on the affected batch using the existing metal detector.
The high delivery pressure meant that an extremely fast and reliable X-ray inspection solution was required. Minebea Intec has been supplying Anona with dynamic and static checkweighers and pre-packaging checking software for 20 years. At that time, the X-ray inspection system was still in the design phase. Being a reliable partner, Minebea Intec quickly arranged to lend Anona a system from its own factory in Aachen.
The system arrived at Anona on a Sunday along with a technician and the Dymond was set up the very same day.
On Monday, the first product tests were carried out and the affected production batch was inspected in the morning. Anona had calculated that the inspection of the batch would take four shifts, but the suspected metal part was reliably detected and eliminated in the very first shift that same day.
The proactive, pragmatic approach in this particular situation enabled Anona to guarantee product quality and meet all delivery deadlines. The food manufacturer has since become the third CCP to implement the Minebea Intec X-ray inspection system Dymond at the end of its production line.
Mediacenter
Category | File Name | File Size | File Type | ||
---|---|---|---|---|---|
Best Practices | |||||
Best Practices | Best Practice // Minebea Intec wins the race against time with its fast X-ray inspection system | 845 KB |