Cheese Manufacturer transform their labelling procedures
Norseland was looking for new ways to automate parts of their manufacturing and reduce the demands on their existing workforce. The WPL-A offered the perfect solution for their labelling processes.
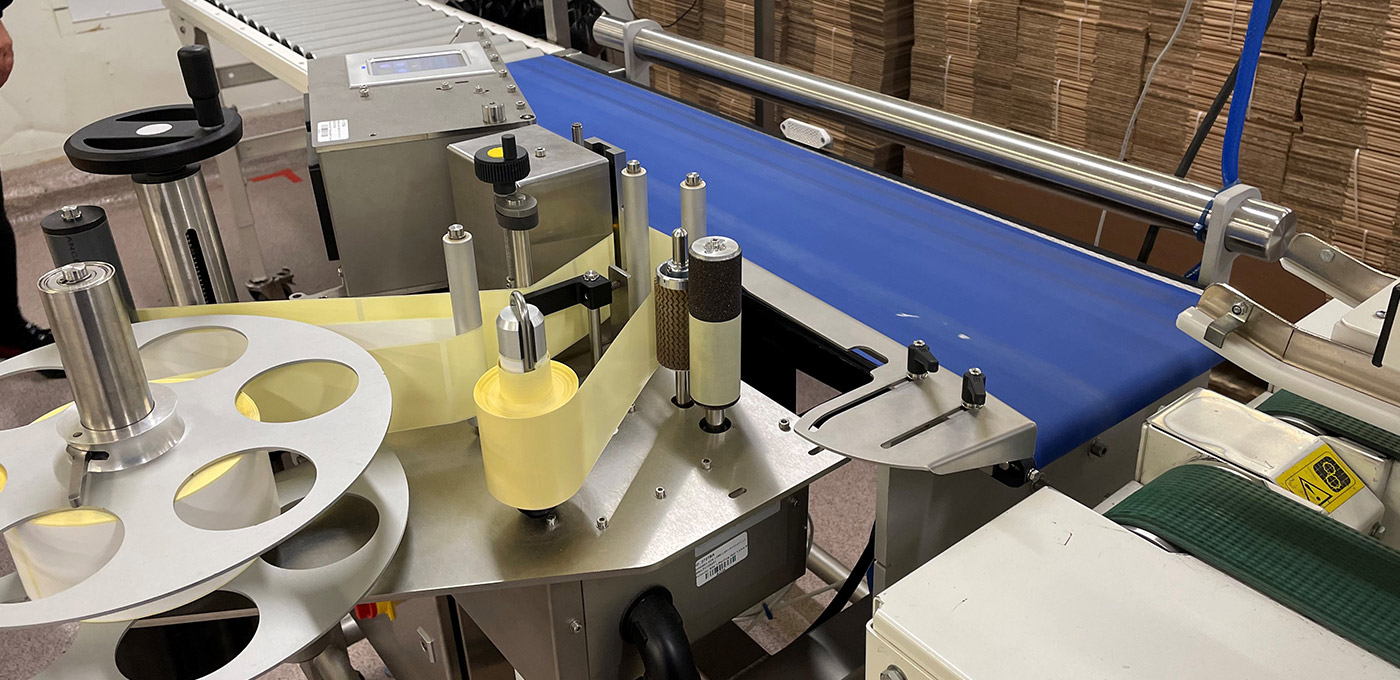
Key facts
Norseland wanted to automate some of their processes in order to increase efficiency and output. The labelling solutions from Minebea Intec not only fullfilled this task, but also helped to increase workplace safety and prepare for future automation.
Application & Product
Norseland Ltd have over 30 Minebea Intec products in use within their manufacturing plant; the most recent additions are the WPL-A and WPL-S. They use them to automate parts of their production.
- Weigh Price Labeller: WPL-A (Automatic)
- Weigh Price Labeller: WPL-S (Static)
Customer benefits
The WPL-A and WPL-S have
- improved the accuracy and efficiency of the labelling processes
- helped to reduce overall production costs
- improved workplace safety
"The WPL-A has transformed the way we do labelling by automating the process. It means we’re getting a much more polished product every time without relying on manpower that we were struggling to source in our vicinity”
Tony Helyar
Continuous Improvement & Capital Projects Manager, Norseland
Norseland has a diverse and versatile offering; providing cheese for every occasion from slices to large blocks and snacking portions. The breadth of their product range relies on a varied range of equipment to manufacture and produce products ready for their customers.
Minebea Intec has been supplying Norseland since 2007 during which time the relationship has gone from strength to strength. They currently have almost 30 Minebea Intec products for various applications in their production, the latest additions being the WPL-A and WPL-S for their labelling requirements.
The requirement for new labelling machinery was driven by the need to automate the process, increase the efficiency and accuracy and also due to a lack of labour in the vicinity of their manufacturing plant. Minebea Intec was chosen as their preferred supplier for a number of reasons; the durability of Minebea Intec products, the hygienic standards of the products, the aftersales service and the ability to adapt products to their exact requirements.
In response to these requirements, the WPL-A was manufactured to accommodate the label sizes required by Norseland and the WPL-S was adapted to fit into their existing line. The WPL-A has also proven to drastically reduce the Health and Safety risks of Repetitive Strain Injury (RSI) of operatives who were previously lifting and handling 1.5kg portions of cheese.
This new machinery is in addition to their existing 16 check weighers; Synus and CoSynus used for end of line legal weight checks and metal detection. They also have EWK portion weighers which control the size of the cheese portions and Flexus’ which are used to control the cutting of the smaller portions of cheese and take a smaller footprint within the factory.
They also have 6 Vistus metal detectors, 2 Combics scales used for sampling for legal records and 1 SPC Enterprise software package which provides real-time reporting on the factory processing.
Mediacenter
Categoría | Nombre del archivo | Tamaño del archivo | Tipo de archivo | ||
---|---|---|---|---|---|
Best Practices | |||||
Best Practices | Best Practice // Un fabricante de queso transforma sus procesos de etiquetado con WPL-A y WPL-S | 975 KB | |||
Video | |||||
Video | Best Practice - Norseland Ltd | 11 B | youtube |