Safety in the dairy industry
X-ray inspection system solves complex quality assurance requirement
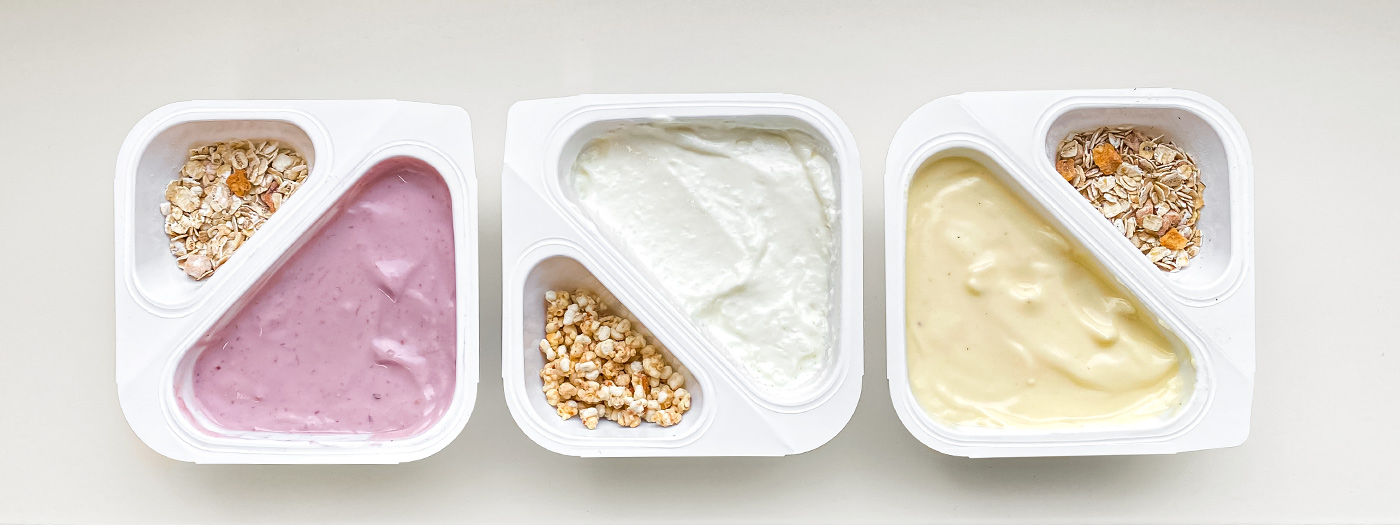
Key facts
The two-chamber tubs are filled with yoghurt and cereal mixtures via a multi-filling system. However, time and again, this causes unwanted clumps of cereal residue to form.
Application & Product
An x-ray inspection system ensures that the products remain free from contamination and contain the ideal cereal consistency.
- X-ray inspection system Dymond 120
Customer benefits
- Maximum detection sensitivity ensures precise inspection
- Reliable detection of different foreign objects and product consistency ensures product quality
- Product teach-in ensures simple and intuitive operation
"The customer was delighted with the result. Through the help of the existing X-ray inspection system Dymond, the customer’s seemingly insurmountable problem – occurring upstream in the filling system – was reliably solved for the long-term."
Markus Leibold
Area Sales Manager Minebea Intec
As part of Minebea Intec’s customer care, regular on-site visits are carried out for all our customers to check that their systems are running smoothly and to collect any feedback. At this customer visit, a particular problem came to light in discussions with the Production Manager. When filling two-chamber tubs with yoghurt and various cereals, time and again there were unwanted, uncontrollable deposits of substandard product residues. The manufacturer pinpointed the problem to the filling process and to the particular properties of the products.
The cereals naturally have a low fat content, which results in the cereal dust adhering to the walls of the filling system chamber. This then clumps and can fall into one of the tubs at any time. The tubs are sealed with an aluminium foil lid straight after filling, so a visual quality control check is out of the question.
The dairy product manufacturer recognised it had an almost unsolvable problem when it came to ensuring product quality. Due to the fact that the two-chamber tubs were sealed with aluminium foil, an X-ray inspection system Dymond from Minebea Intec was already integrated into the packaging line at the detection point for foreign objects. The sales team sought the advice of Minebea Intec’s X-ray technology experts and together they developed a solution – with help from the x-ray inspection system.
The advanced Dymond system doesn’t just detect a wide variety of foreign objects, such as glass, stone or metal, but it can also recognise deviations in a product’s consistency. Together, the system’s settings were successfully modified. Since then, the system has reliably removed not only contaminated products from the product flow but also substandard products.
Mediacenter
Categorie | Bestandsnaam | Bestandsgrootte | Bestandstype | ||
---|---|---|---|---|---|
Best Practices | |||||
Best Practices | Best Practice // An X-ray inspection system from Minebea Intec tackles even the most complex requirements in yoghurt production | 1,28 MB | |||
Best Practice // Cheese Manufacturer transform their labelling procedures using the WPL-A and WPL-S | 855 KB | ||||
Video | |||||
Video | Explainer Video Dairy Industry | 11 B | youtube | ||
Best Practice - Norseland Ltd | 11 B | youtube |